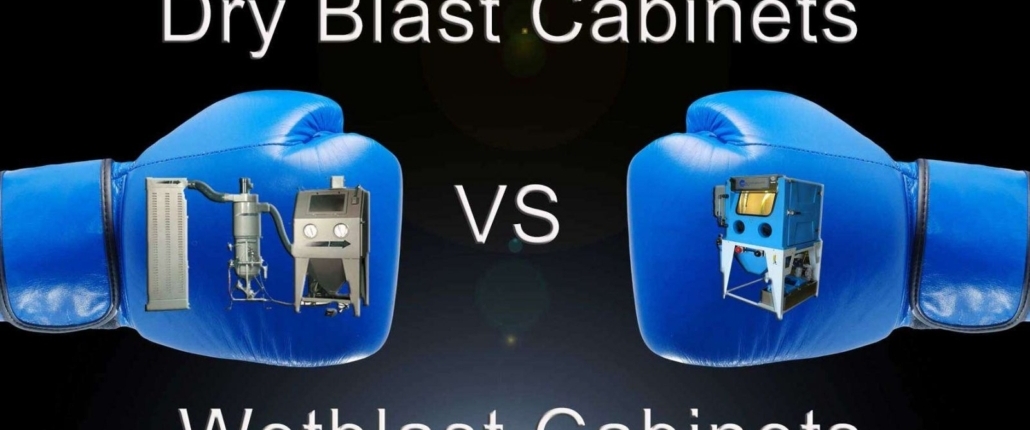
When it comes to the best blasting system for the job there are several variables to consider, including suction vs pressure blast systems, media type, budget, desired surface finish, etc.
So let’s look at some of the advantages and disadvantages of Dry Blasting vs Wet Blasting in a blast cabinet for an industrial environment. This will be a good place to start the discussion, knowing that detailed testing is available to fully determine specifics for an application.
When it comes to the best blasting system for the job there are several variables to consider, including suction vs pressure blast systems, media type, budget, desired surface finish, etc.
So let’s look at some of the advantages and disadvantages of Dry Blasting vs Wet Blasting in a blast cabinet for an industrial environment. This will be a good place to start the discussion, knowing that detailed testing is available to fully determine specifics for an application.
Dry Blasting Cabinet Advantages
- Equipment is more economical
- Dry blasting is more aggressive, typically faster than wet blasting
- No drying is required
- Less corrosion issues
- More aftermarket parts available
- Can use steel shot and grit
- Easier to clean out vs some wet blast systems that do not have a drain plug system
- The slurry cushions the process and can eliminate embedded abrasive.
- Finer finishes can be achieved with the wet blast process.
- The wet blasting process is Dust Free—equipment can be installed in clean work cells to closely control Q/A. Risk of dust fires and explosions eliminated!
- Parts can be loaded wet, or even with oil or grease.
- Water helps remove greases and oils from surfaces.
- Oil can be eliminated from the system with an optional oil separator.
- Heat can be added to a system to speed up cleaning.
- Capabilities to wet blast, rinse, and even dry parts in one system.
- Wet blast cabinets provide closed loop processing and filtered water for rinsing.
- Media life is increased, wet blasting reduces the media breakdown rate by as much as two thirds compared to traditional dry blasting.
- No Dust Collector—Smaller Footprint.
- Static Free
Wet Blasting Cabinet Advantages
Should You Choose Wet Blasting or Dry Blasting?
A lot depends on the application and your budget.
Dry blasting has been used for decades and for as many different industrial applications as you can think of. When it comes to wet blasting, below are some of the applications where this process excels.
- Medical Parts – especially when ferrous contamination and media embedment are concerns
- Aerospace – composite etching (provides a gentle even finish) and bonding (can increase bond strength up to 200x when compared to traditional methods)
- Automotive – ideal when oily, greasy, or carbon stained parts need to be cleaned and finished
- Firearms – Provides an even finish and can be used to get into hard to reach places
Still need help deciding between wet blasting vs dry blasting?
Reach out and talk to our team of trained technical reps. We will find the best solution for your application based on cost, process and facility requirements.
Lab Testing
Midvale offers full lab testing services to prove an application process. We can test the type of machine, various pressures, and media to determine the best process solution. Ask us about these services today!