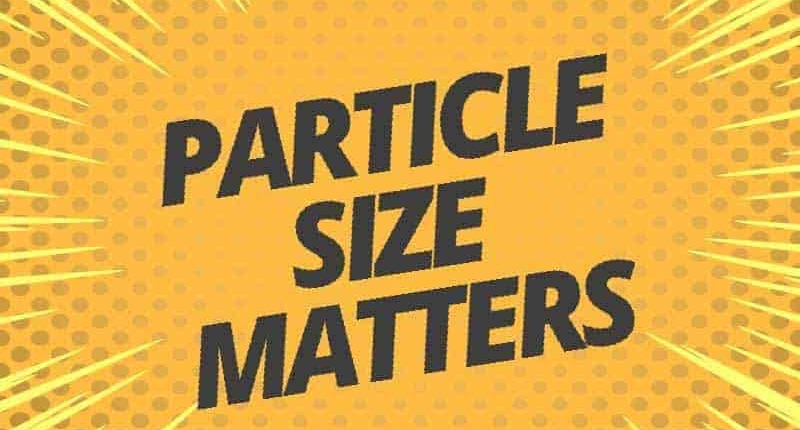
There are many different sizing options available when choosing the right abrasive for your application. So where do you start? One option is to determine what mil profile is required for the coating or paint that will be applied after blasting. Many coating manufacturers have information indicating the required mil profile needed to have their coating adhere properly to the surface. Also likewise many abrasive manufacturers have charts like the one below that provide a range of mil profile that can be achieved with a given size.
Another factor to consider is the hardness of the abrasive and the material being blasted. Many abrasive mfgs indicate where their material falls on the Mohs scale (a hardness scale) on their tech data sheets. 1 on the scale being the softest like talc and 10 being the hardest like diamond. The harder the abrasive the higher likelihood of the abrasive changing the surface being blasted. See media guide to compare common abrasives.
Now that we have looked at hardness and mil profile’s effects on the surface being blasted, let’s look at particle size distribution. Most abrasives sold today fall within a range of grain sizes. These grain sizes are measured and separated on screens and are referred to as mesh sizes. For instance on the mil profile chart below for Green Diamond Sand you see sizes like 8X16 or 16X36, these numbers indicate that the majority of grains in that size fall within those mesh sizes. There are also a small percentage of grains that are smaller or larger than those mesh sizes typically found in the mix.
Working Blast Mix
Once you have chosen the blast media you are going to use based on the criteria above, you need to now maintain a working mix if you are recycling and reclaiming your media. To do this turn off the dust collection system or cap off the bottom of the blast cabinet and collect the media after cycling and then screen it (utilizing it in a Ro-tap machine, our lab can help you with screening) both before cycling and then after the first cycle.
Screening Your Media
After you have screened the media then you can see determine how quickly the media is breaking down. Compare the your results to a sizing curve like the one above (provided by your vendor or an abrasive mfg), then determine what percentage of media is falling outside of the curve after is has been screened. Once you make that calculation then you can add that percentage of media back into your cabinet after every cycle if possible or over a given time period of blasting. There are systems that you can use to auto feed media back into your system where parameters are critical.
To understand roughly how much media you going through within a given period of time, you may want to use this chart since cycles can be hard to determine while continuously blast. Below is an abrasive consumption chart that shows how much media is going through your nozzle (based on nozzle size and pressure) within a given amount of time.
Get In Touch
Talk to our team today about how you can improve your blasting operation. We have resources that can guide you on which media and particle size you should be using in your blasting process.