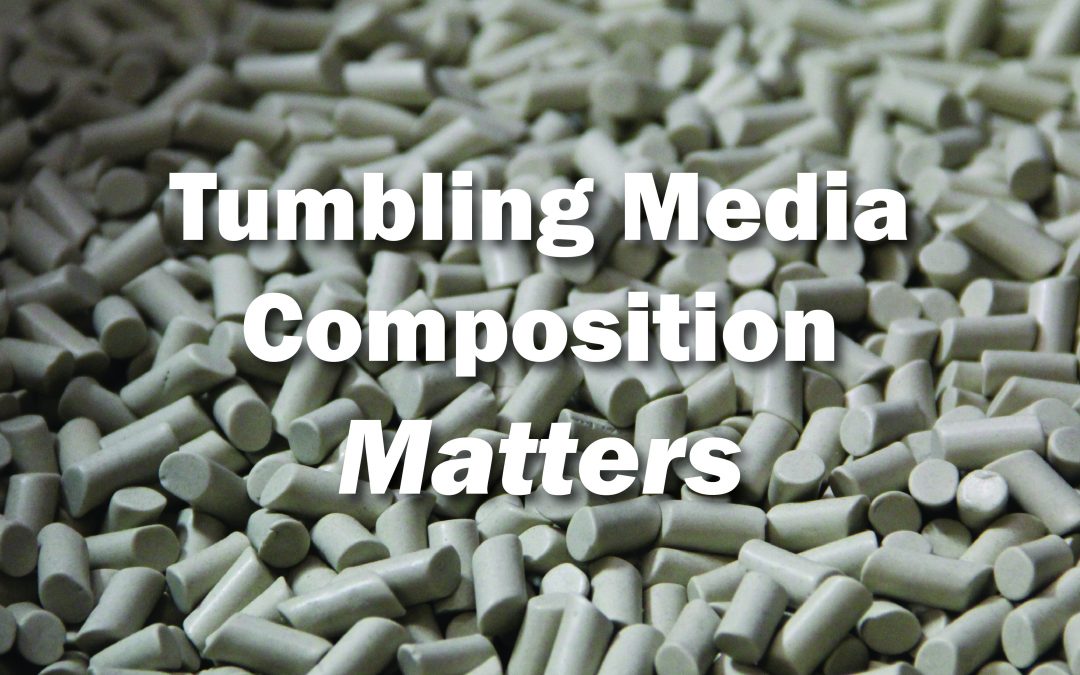
Tumbling Media Composition Matters
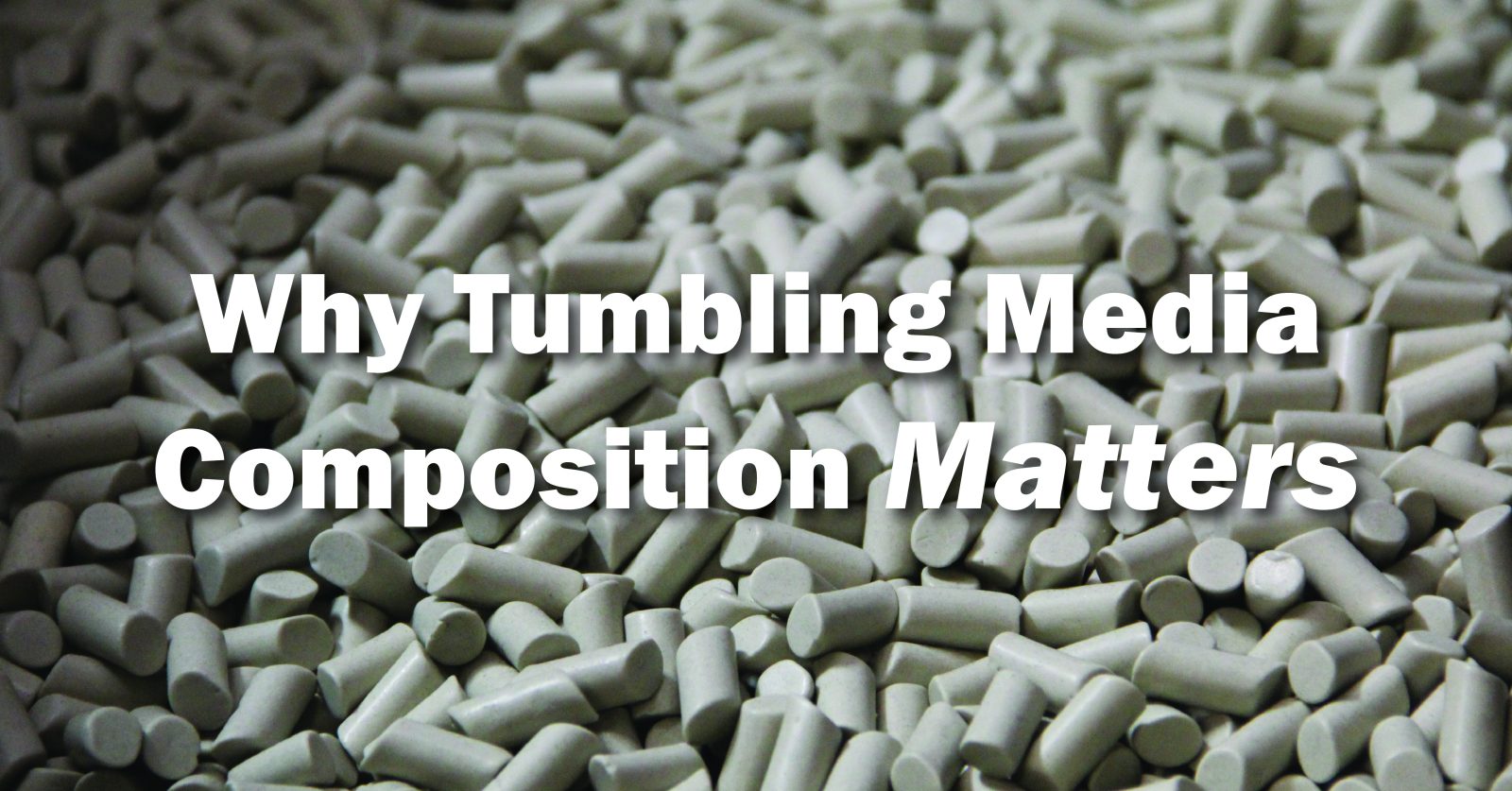
Tumbling Media Composition Matters
A Media Composition Resource Guide
The composition of tumbling media plays an important role in your finishing process and determines whether the media is for cutting or finishing. Cutting media will contain abrasives within the composition while, finishing media will either contain no abrasive or very fine abrasive. The main materials used for tumbler media include ceramic, steel, plastic, urethane, or corn cobs.
Ceramic Tumbling Media
Ceramic media is typically made up of a combination of abrasive and clay. The curing time and oven temperatures determine the hardness of the ceramic. A softer ceramic will provide better cutting as the media wears away revealing fresh abrasive under the top layer. There are various cutting speed options available to meet specific finishing requirements.
Applications: Deburring, Deflashing, Burnishing, Polishing, Brightening, Radiusing
Available Shapes: angle cut cylinders, stars, cones, triangles, wedges, pyramids, and specialty shapes upon request.

Stainless Steel Tumbling Media
Steel media provides shape uniformity, short cycle times, and long-lasting durability. Often used in cosmetic finishing, steel tumbling media does not scratch or damage the parts, but provides a clean surface. Steel media does not cause wear to the machine lining, reducing maintenance costs.
Applications: Stress Relieving, Strengthening, Brightening, Preplate
Available Shapes: pins, ball cones, oval cones, diagonal cylinders, and specialty shapes upon request.



Plastic Tumbling Media
Plastic media has a lower density than ceramic and is typically softer. The composition is made of abrasive, bonded with various types of plastic or resins. Plastic is commonly used in applications with softer metals or fragile parts. There are various cutting speed options available to meet specific finishing requirements.
Applications: Deburring, Deflashing, Surface Metal Removal, Fine Finishing, Radiusing
Available Shapes: angle cut cylinders, stars, cones, triangles, wedges, pyramids, and specialty shapes upon request.


Urethane Dry Finishing Media
Urethane media eliminates the need for compound in the tumbling process. It has a long-life cycle and reduces many typical use costs. It also eliminates the messy residue often associated with plastic media formulations.
Applications: Deburring, Deflashing, Burnishing, Polishing, Brightening
Available Shapes: angle cut cylinders, stars, cones, triangles, wedges, pyramids, and specialty shapes upon request.


Corn Cob Tumbling Media
Corn cob media is typically used to dry metal parts after tumbling or parts washing cycles. The starch helps absorb water, oil and grit. This reduces the chance for watermarks or stains on the parts. It can also be infused with various buffing and polishing compounds for enhanced finishes.
Applications: Deflashing, Burnishing, Polishing, Brightening
Available Shapes: crushed corn cobs, multiple sizes available


Selecting the Right Media Composition
The desired finishing process or final outcome is a large factor in determining the composition as some media types are more suitable for certain applications than others. When selecting your tumbling media composition, as well as shape/size, the part and desired outcome are major factors. The type of metal is a factor when selecting composition as softer metals need a specific blend for ceramic, as an example.
Process Testing
Testing your tumbling process is vital for selecting the right media. Send us your parts and our processing lab will determine the right media shape and type for your finishing application.
Recent Comments